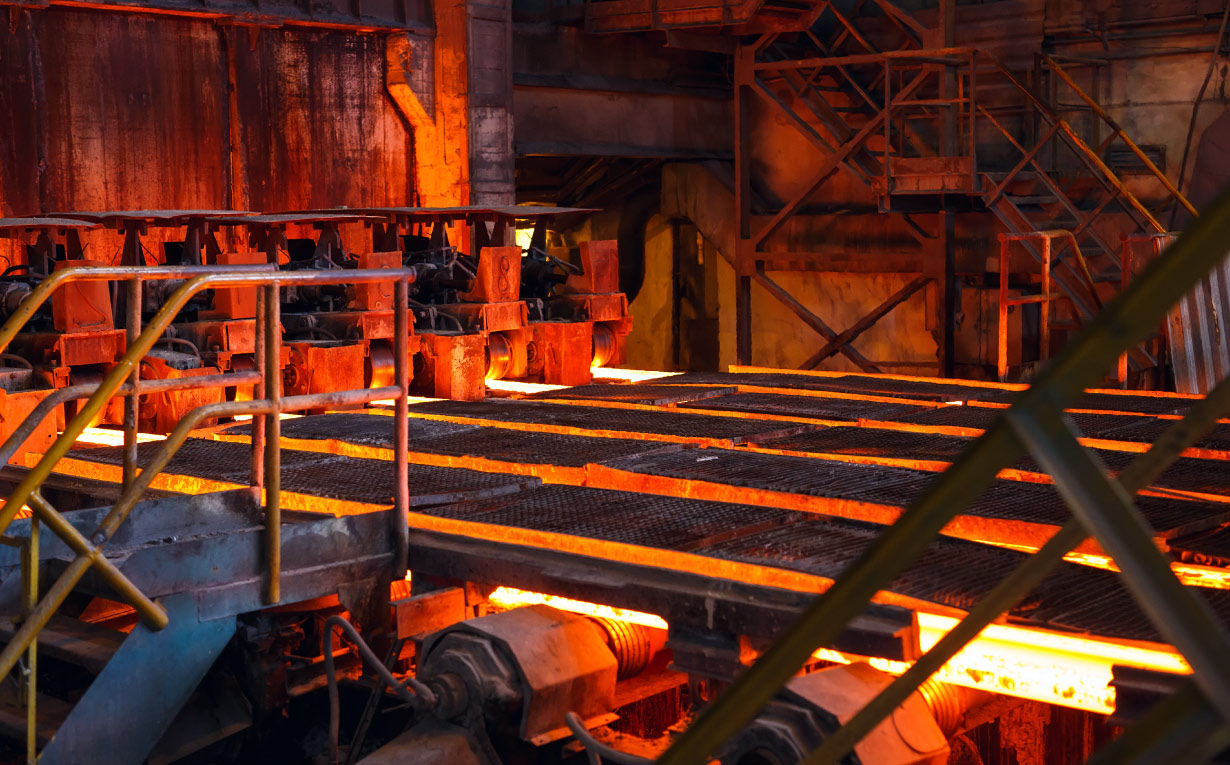
Forgital – Velo d’Astico Plant
The Forgital Group, an Italian industrial excellence with a strong international vocation, is recognised globally for the production of seamless hot-rolled rings in steel and titanium alloys, destined for strategic sectors such as aerospace, oil & gas, energy, mechanical and manufacturing. With an export share of over 80%, Forgital has always invested intechnological innovation and operational sustainability as competitive assets for its growth.
In 2013, the plant in Velo d’Astico (VI) embarked on an ambitious lighting redevelopment project, entrusting Quantum with the design and testing of an intelligent and highly resistant LED lighting system, capable of operating in extreme environmental conditions, typical of steelmaking departments: high temperatures, the presence of rolling mills, industrial presses and strong electromagnetic interference.
The pilot project, which started in August 2013, was an extremely challenging technical test-bed for Cree’s luminaires, selected for their robustness, and for Quantum’s QLight™ management system, developed to ensure flexibility, efficiency and continuous monitoring of luminous fluxes even in difficult environments.
The success of the initial phase led to the complete replacement of over 600 lighting points by the end of 2014, with the full adoption of the QLight™ system within the production departments. The benefits were immediate and measurable: a reduction in energy consumption of 1.3 Gigawatt-hours per year, an environmental saving of over 4,000 tonnes of CO₂ less emitted into the atmosphere each year, equivalent to the effect of 20,000 trees planted, symbolically one for each year of work for each of the group’s 1,000 employees.
The project continued in 2015 with the redevelopment of the outdoor areas, including the lighting towers in the forecourt, equipped with 240 LED Cree HOs, and the complete digitisation of the plant control through Quantum’s Industrial Internet of Things platform. This software enables intelligent lighting control, adapted to the production cycle, staff presence, daylight and operating conditions in real time.
To crown the path undertaken, in December 2014 the plant obtained the prestigious ISO 50001 certification, confirming the effectiveness of the energy management strategies and the concrete attention paid to the environment, process efficiency and responsible use of natural resources.An emblematic intervention for Italian heavy industry, which has shown how even in energy-intensive sectors it is possible to combine innovation, performance and sustainability, demonstrating industrial vision and the ability to lead towards a more efficient and responsible future.
- Lighting study in environments with high thermal and magnetic stresses
- Installation of more than 600 highly resistant LED luminaires
- Integration with QLight™ control and management system
- IIoT software application for intelligent monitoring and control of luminous fluxes
- Support in achieving ISO 50001 certification